Finite Element Analysis Assisted Improvement of Ionic Polymer Metal Composite Efficiency for Micropump of 3D Bioprinter
DOI:
https://doi.org/10.22034/advjscieng21021023Keywords:
Bioprinter, Micropump, IPMC, Piezoelectric, Finite element analysisAbstract
Nowadays, smart materials for manufacturing bioprinters have diverse usages; micropump is one other product resulted by using smart materials such as IPMC, piezo, and etc., in manufacturing above mentioned printers. This item has an important role in micro systems and delivering special fluid such as nanofluids. In order to manufacture this type of pump a wide range of materials can be used. In this research, a smart material named ionic-polymer-metal composite (IPMC) is used; however, the current material for them is piezoelectrics. IPMC systems are mostly used in micro pump diagrams because of their self-assessment feature, low starting voltage, and elastic structure. In order to increase the IPMC actuator’s durability and also enlarging the deformation range, a new design for IPMC diaphragms is introduced in this paper. In prevalent designs, all the actuator edges where clamped, but here different IPMC actuators in circular and triangular shapes are presented. And also the new design allows the solvent to completely cover the diaphragm by separating the fluid from IPMC. IPMC strain and stresses are modeled in order to analyze the efficiency of the new design. The results show that the presented designed IPMC works steadily for a longer duration of time. It also has a wider deformation range and more efficiency compared to the conventional design.
References
Ghani M, Soleimanimehr H, Shirani Bidabadi E. An investigation the effect of Acidithiobacillus ferrooxidans bacteria on biomachining of titanium alloy and copper. Journal of Modern Processes in Manufacturing and Production. 2020;9:25-32.
Hossein-Fakhrzade R I. “An introduction to biological printing as a new method in tissue engineering. Iran diabetes and Lipid Magezin. 2011.
Farshchi Yazdi SA, Corigliano A, Ardito R. 3-D design and simulation of a piezoelectric micropump. Micromachines. 2019;10:259.
Biniyazan F, Soleimanimehr H. Improving both strength and ductility of Al-7075 by combining dual equal channel lateral extrusion with aging heat treatment. Iranian Journal of Science and Technology, Transactions of Mechanical Engineering. 2021; in press.
Soleimanimehr H, Nategh MJ, Najafabadi AF, Zarnani A. The analysis of the Timoshenko transverse vibrations of workpiece in the ultrasonic vibration-assisted turning process and investigation of the machining error caused by this vibration. Precision Engineering. 2018;54:99-106.
Soleimanimehr H. Analysis of the cutting ratio and investigating its influence on the workpiece’s diametrical error in ultrasonic-vibration assisted turning. Proceedings of the Institution of Mechanical Engineers B. 2021;235:640-649.
Soleimanimehr H, Hosseini Z, Habibi M, Goortani BM. Energy harvesting from wind by piezoelectric for autonomous remote sensor. Advanced Journal of Science and Engineering. 2020;1:80-85.
Mohith S, Karanth PN, Kulkarni SM. Recent trends in mechanical micropumps and their applications: a review. Mechatronics. 2019;60:34-55.
Truong DQ, Ahn KK, Nam DN, Yoon JI. Identification of a nonlinear black-box model for a self-sensing polymer metal composite actuator. Smart Materials and Structures. 2010;19:085015.
Haq M, Gang Z. Ionic polymer–metal composite applications. Emerging Materials Research. 2016;5:153-164.
Almomani A, Hong W, Hong W, Montazami R. Influence of temperature on the electromechanical properties of ionic liquid-doped ionic polymer-metal composite actuators. Polymers. 2017;9:358.
Chaudhari SV, Chakrabarti MA. Modeling of concrete for nonlinear analysis using finite element code ABAQUS. International Journal of Computer Applications. 2012;44:14-18.
Mirzaei M. Making sense the ideas in silico. Lab-in-Silico. 2020;1:31-32.
Mirzaei M. Science and engineering in silico. Advanced Journal of Science and Engineering. 2020;1:1-2.
Soleimanimehr H, Mirzaei M. An introduction to lab-in-silico. Lab-in-Silico. 2021;2:1-2.
Zolfagharian A, Kouzani AZ, Khoo SY, Moghadam AA, Gibson I, Kaynak A. Evolution of 3D printed soft actuators. Sensors and Actuators A. 2016;250:258-272.
Nisar A, Afzulpurkar N, Mahaisavariya B, Tuantranont A. MEMS-based micropumps in drug delivery and biomedical applications. Sensors and Actuators B. 2008;130:917-942.
Bar-Cohen Y, Bao X, Sherrit S, Lih SS. Characterization of the electromechanical properties of ionomeric polymer-metal composite (IPMC). Smart Structures and Materials. 2002;4695:286-293.
Chen Z, Tan X. A control-oriented and physics-based model for ionic polymer-metal composite actuators. IEEE/ASME Transactions on Mechatronics. 2008;13:519-529.
Chen Z, Hedgepeth DR, Tan X. A nonlinear, control-oriented model for ionic polymer-metal composite actuators. Smart Materials and Structures. 2009;18:055008.
Nemat-Nasser S, Li JY. Electromechanical response of ionic polymer-metal composites. Journal of Applied Physics. 2000;87:3321-3331.
Nemat-Nasser S. Micromechanics of actuation of ionic polymer-metal composites. Journal of applied Physics. 2002;92:2899-2915.
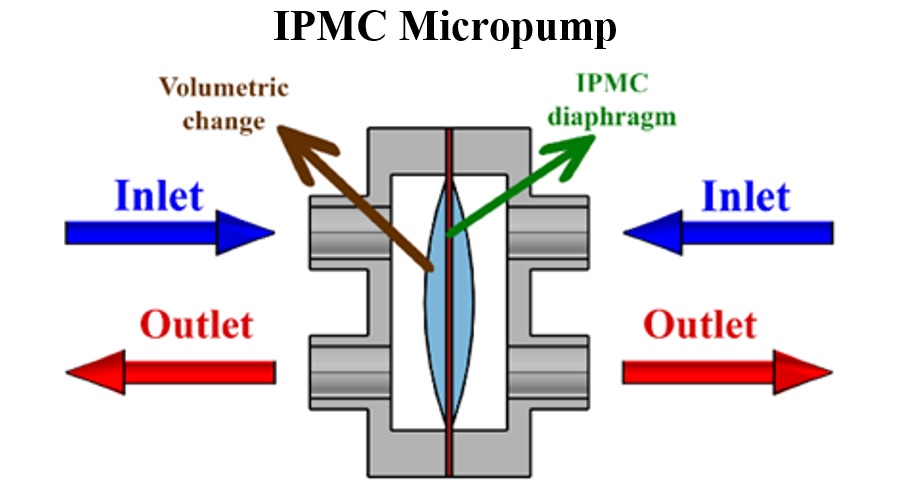
Downloads
Published
How to Cite
Issue
Section
License
Copyright (c) 2021 Advanced Journal of Science and Engineering

This work is licensed under a Creative Commons Attribution 4.0 International License.
This work is licensed under a Creative Commons Attribution 4.0 International License (CC-BY 4.0).